Essential Insights for Sourcing Mechanical Lifts in a Global Market
In today's global marketplace, the demand for mechanical lifts is witnessing an unprecedented surge, driven by the rapid urbanization and the booming construction sector. According to a report by Research and Markets, the global mechanical lifts market is projected to grow at a compound annual growth rate (CAGR) of 7.1% from 2021 to 2028, reflecting the critical role these systems play in enhancing operational efficiency and safety in various industries. As urban centers expand and infrastructure projects increase, sourcing the right mechanical lift has become an essential consideration for businesses aiming to optimize their logistics and accessibility.
However, navigating the complexities of sourcing mechanical lifts in a global market poses significant challenges, including regulatory compliance, quality assurance, and supplier reliability. A study by Technavio highlights that 48% of companies report difficulties in identifying reputable suppliers, while ensuring that these lifts adhere to stringent safety standards. As such, acquiring in-depth insights into market dynamics, technological advancements, and regional compliance is imperative for stakeholders. This blog aims to provide essential insights to effectively navigate the landscape of mechanical lift sourcing, ensuring businesses can make informed decisions that align with both their operational needs and safety standards.
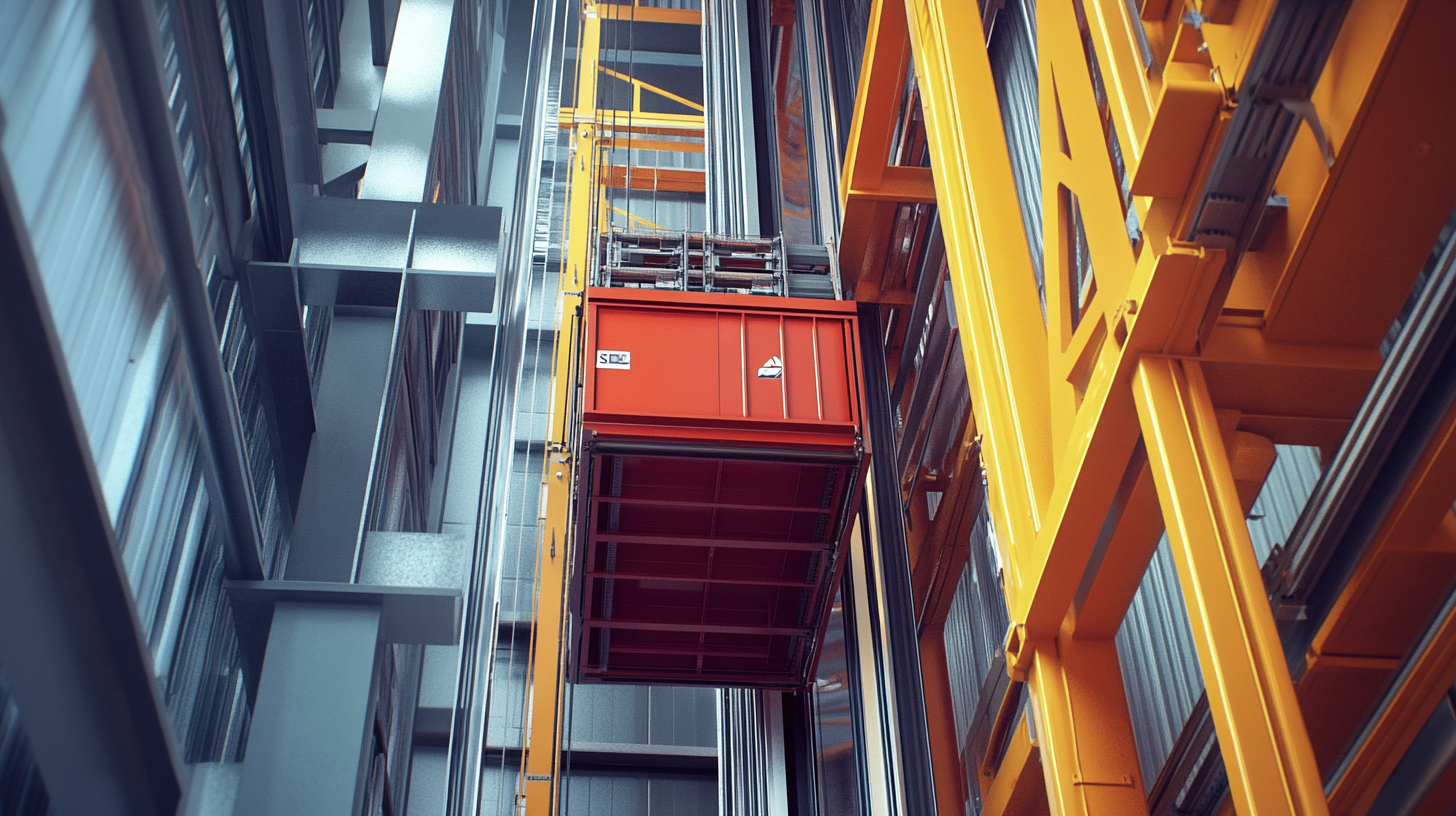
Understanding the Different Types of Mechanical Lifts for Global Applications
When sourcing mechanical lifts for global applications, it is crucial to understand the various types available and their specific uses. Mechanical lifts can be categorized into several types, each designed to cater to different needs in diverse environments. For instance, hydraulic lifts are prevalent in warehouses and factories due to their ability to handle heavy loads efficiently. They are particularly favored for their robust design and smooth operation, making them ideal for transporting goods and materials. On the other hand, electric lifts are gaining traction in commercial and residential settings. Their compact design and ease of use make them perfect for smaller spaces. Electric lifts often feature advanced safety mechanisms and energy-efficient systems, aligning with the growing demand for environmentally friendly solutions. In addition, pneumatic lifts, although less common, are excellent choices for environments requiring clean and quiet operations, such as hospitals and cleanrooms. Understanding these distinctions not only aids in selecting the right lift for a specific application but also ensures compliance with regional regulations and standards. As mechanical lifting solutions continue to evolve, staying informed about the latest technologies and innovations becomes essential for businesses looking to optimize their operations globally.
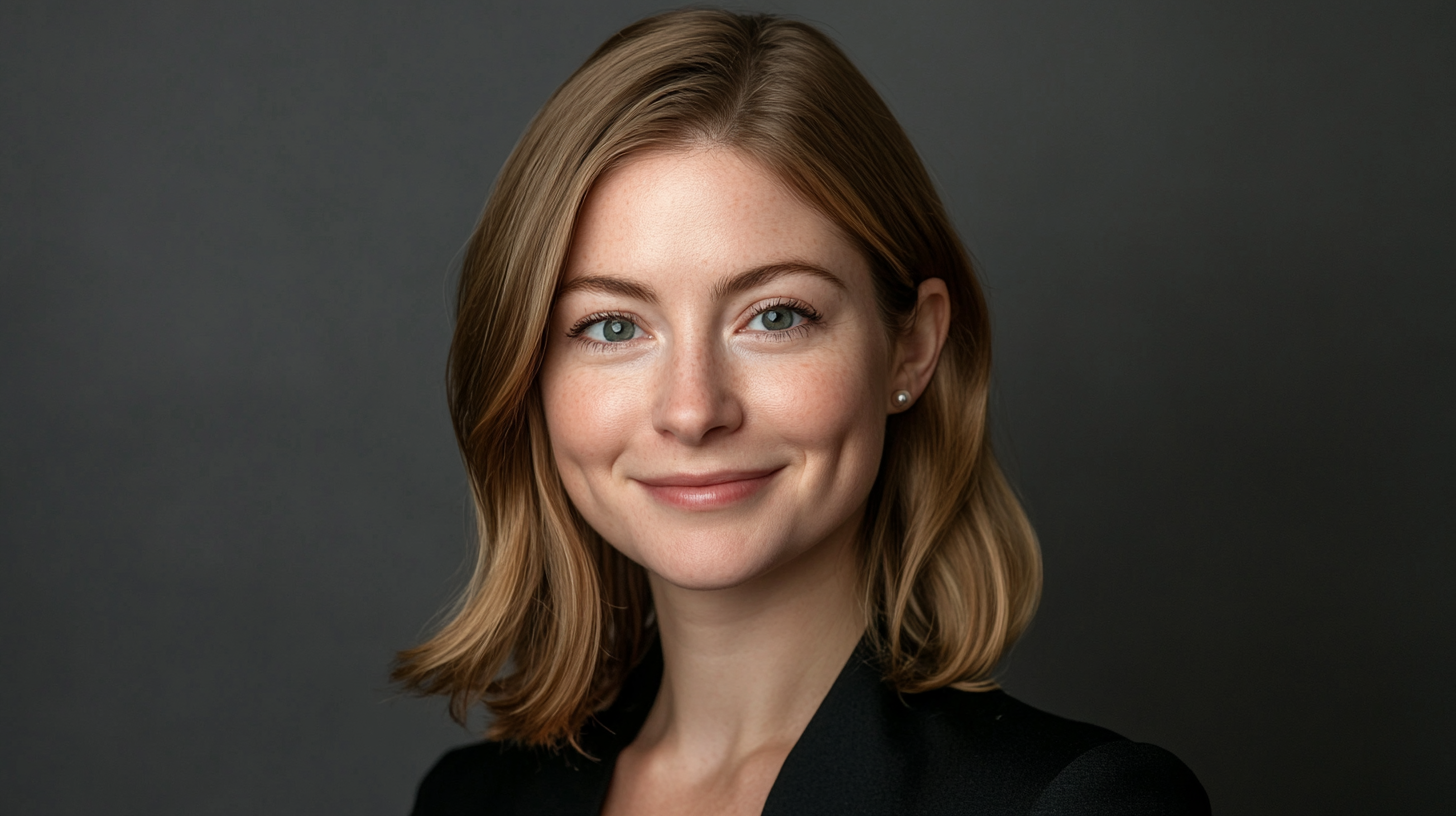
Key Factors to Consider When Sourcing Mechanical Lifts Internationally
When sourcing mechanical lifts in a global market, several key factors must be meticulously considered to ensure optimal performance and efficiency. One primary concern is energy consumption, which plays a pivotal role in the sustainability and operational costs of elevator systems. Recent studies highlight the significance of selecting elevators with lower energy consumption rates, contributing not only to cost savings but also aligning with escalating environmental regulations worldwide.
Moreover, the integration of advanced technology in mechanical lifts has transformed the way vertical transportation is approached. Innovations in elevator design and functionality can significantly enhance user experience and building efficiency. When evaluating suppliers, it is crucial to inquire about the latest advancements in elevator technology and how they can be adapted to meet the specific needs of your project.
Another critical aspect is understanding the regional compliance and safety standards. Different countries may have varying regulations regarding elevator installation and maintenance. Ensuring that your chosen supplier is well-versed in local standards will mitigate risks and enhance the reliability of your lift systems. These considerations ultimately contribute to a comprehensive sourcing strategy, positioning projects for future success in an increasingly competitive global market.
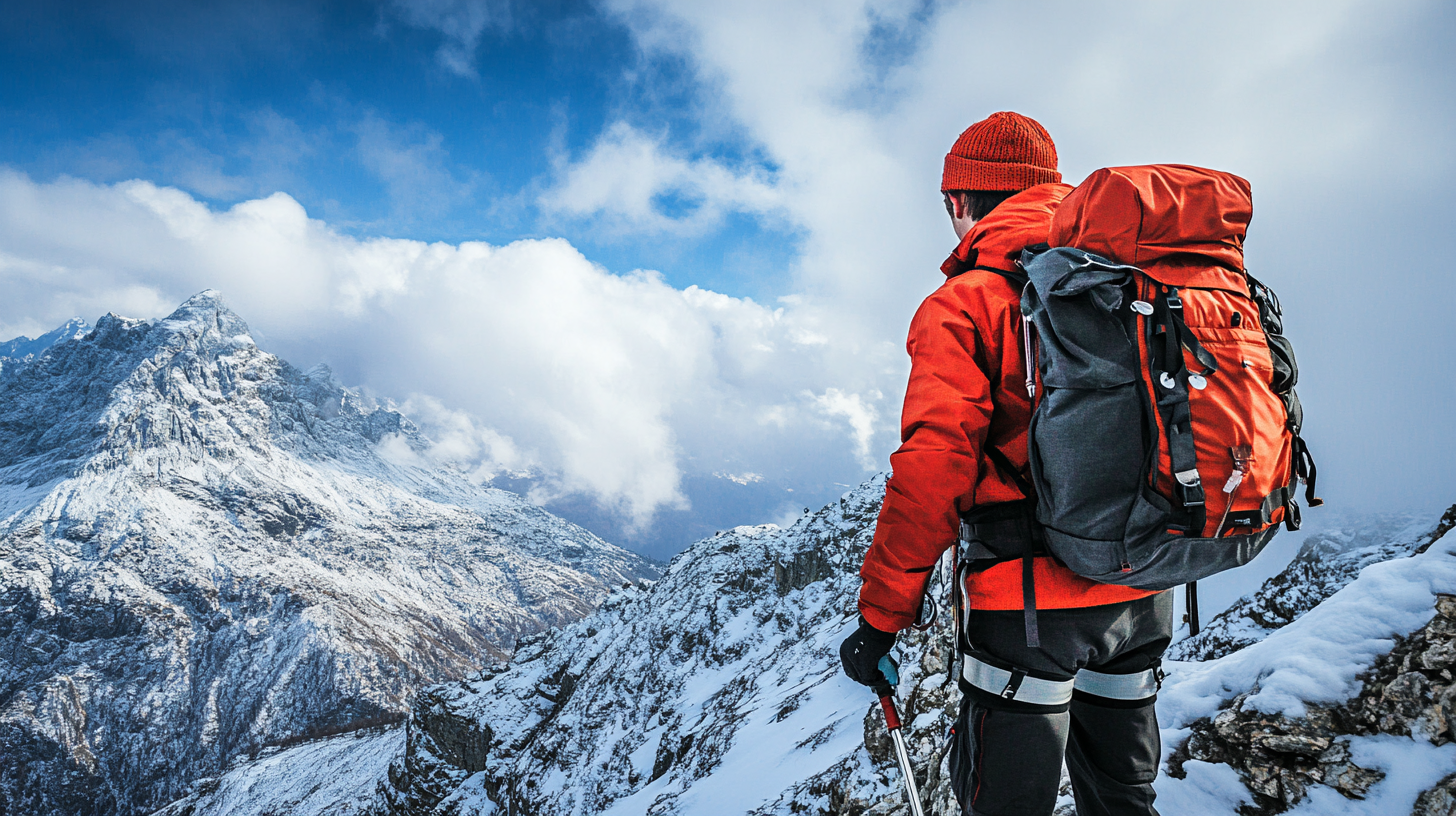
Navigating Regulations and Compliance Standards in Mechanical Lift Procurement
When sourcing mechanical lifts in a global market, navigating regulations and compliance standards is pivotal for procurers and businesses alike. Each country has its own set of laws governing the design, installation, and usage of mechanical lifts, which can significantly affect procurement processes. Understanding these regulations ensures that the mechanical lifts obtained meet local safety standards and operational requirements, thereby minimizing the risk of legal complications and enhancing employee safety.
Moreover, compliance with international standards, such as those set by the International Organization for Standardization (ISO) or the American Society of Mechanical Engineers (ASME), is critical for companies looking to extend their market reach. These standards provide a framework that covers every aspect of lift design and functionality, from load capacity to emergency procedures. Companies must thoroughly assess how these standards apply in their specific operational contexts, as failure to comply can result in penalties or costly redesigns.
Additionally, engaging with local experts and regulatory bodies can provide invaluable insights. Local consultants can help navigate the complexities of regional compliance, ensuring that procurement processes are efficient and aligned with legal expectations. Ultimately, a proactive approach to understanding and integrating these regulations not only streamlines mechanical lift procurement but also fosters a culture of safety and quality within organizations operating on a global scale.
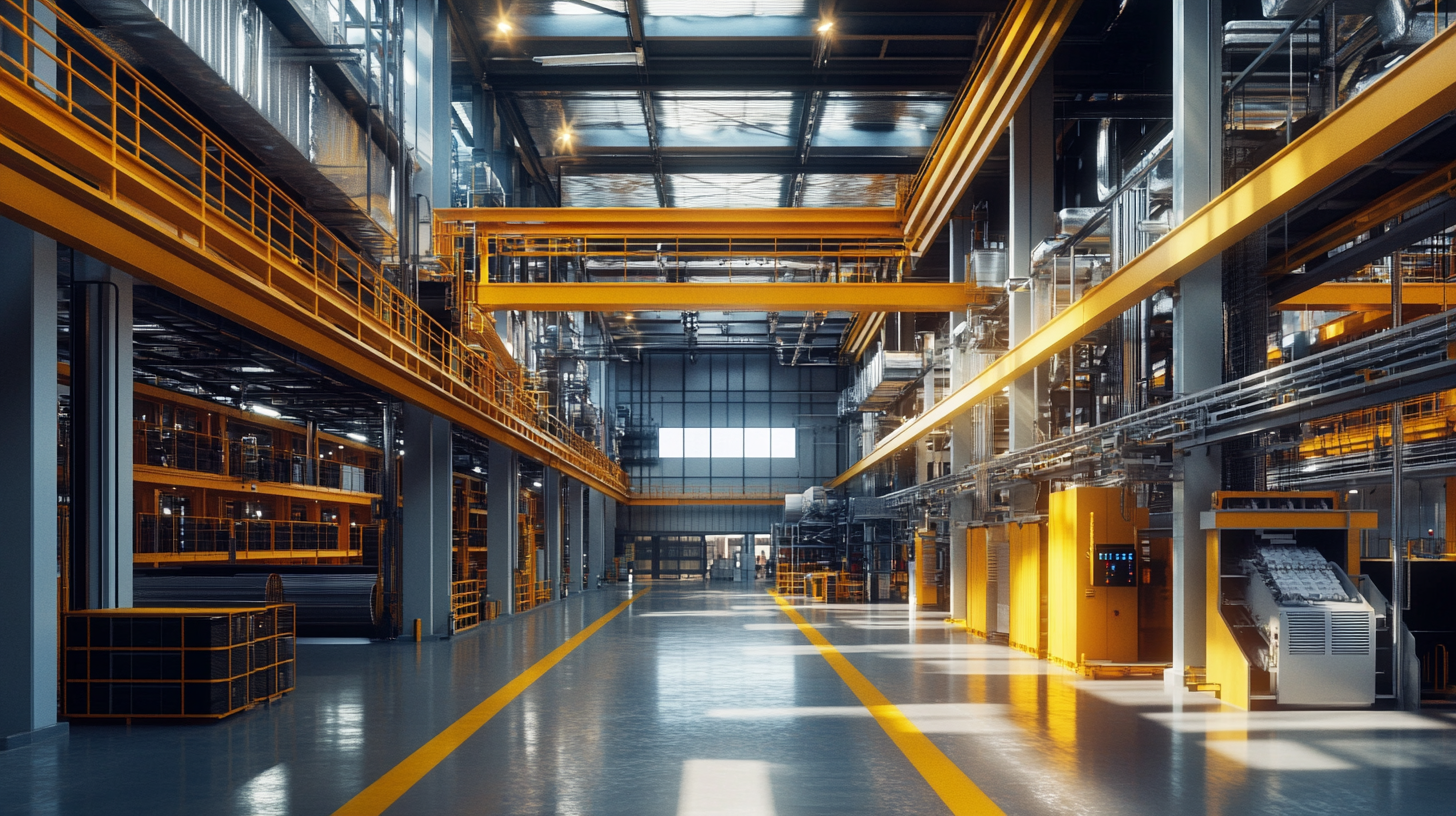
Evaluating Supplier Reliability and Quality in the Global Marketplace
When sourcing mechanical lifts in a global market, evaluating supplier reliability and quality is paramount. Suppliers are not just vendors; they are partners in ensuring operational efficiency and safety. An effective assessment begins with examining a supplier’s track record. Look for certifications such as ISO standards and industry-specific qualifications that indicate adherence to manufacturing excellence. Companies that have invested in quality management systems are often more reliable, as they prioritize consistent output and customer satisfaction.
Additionally, conducting comprehensive due diligence involves understanding the supplier’s financial stability. A reliable supplier should showcase a stable history of performance, which often includes positive client feedback and a strong portfolio of past projects. Engaging in direct conversations with references can provide deeper insights into their reliability. Moreover, assessing their production capabilities, lead times, and responsiveness to inquiries can reveal much about their operational practices and commitment to delivering quality products.
Finally, it is crucial to cultivate transparency in communication. Suppliers who are open about their processes, challenges, and quality control measures often reflect a higher degree of reliability. Establishing a collaborative relationship by discussing expectations, milestones, and after-sales support can further enhance the partnership. By prioritizing these evaluations, businesses can confidently navigate the complexities of a global supply chain and secure reliable suppliers for their mechanical lift needs.
Cost-Benefit Analysis: Assessing Investment in Mechanical Lifts for Your Business
When considering an investment in mechanical lifts, conducting a thorough cost-benefit analysis is paramount for businesses operating in a competitive global market. Mechanical lifts, while often seen as a significant upfront expense, can deliver considerable long-term benefits that enhance operational efficiency. By evaluating the initial costs associated with purchasing and installing mechanical lifts versus their potential to increase productivity, minimize downtime, and reduce labor costs, businesses can make informed decisions that align with their financial goals.
One of the critical components of this analysis involves understanding the various types of mechanical lifts available and their respective costs. From hydraulic lifts to electric lifts, each type offers different advantages and operating expenses. Additionally, businesses need to assess the maintenance and operational costs associated with each option. By factoring in these variables, companies can project the return on investment (ROI) over time, which will be instrumental in justifying the expenditure.
Another essential element of the cost-benefit analysis is to consider how mechanical lifts can enhance safety and compliance within the workplace. Investing in modern mechanical lift solutions not only prevents potential workplace accidents but also helps organizations meet regulatory standards. By reducing the risk of injuries, businesses can save significantly on potential liability claims, workers’ compensation costs, and ensure a safer environment for their employees, ultimately leading to higher staff morale and retention.
In summary, a comprehensive cost-benefit analysis not only evaluates the financial aspects of investing in mechanical lifts but also highlights the strategic advantages they provide. Businesses must look beyond the initial purchase price and assess how these lifts can catalyze efficiency, safety, and long-term savings in an increasingly competitive market.